6mm Hardiebacker 250 Cement Floor Board
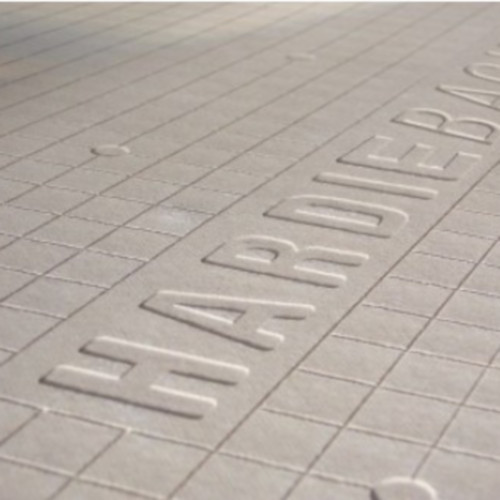
- Product Code: A1-1160
- Delivery Time: 2 - 4 days
- Brand: James Hardie
- Model and Size: 1200mm x 800mm - 0.96m2
- Weight: 9.00kg

4.7 out of 5 - Excellent
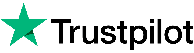

6mm Hardiebacker 250 Cement Floor Board
6mm Hardiebacker 250 is backboard used as an ideal substrate for vinyl, natural stone and ceramic tiles, especially designed for floors and countertops. It can be used even for masonry walls, able to withstand loads of up to 100kg/m2. It consists of cement, cellulose, sand and selected additives, but doesn't contain asbestos, formaldehyde or gypsum, which can disintegrate when exposed to high levels of moisture. It is the perfect for wet areas such as bathrooms or kitchens.
The boards 6mm thickness helps minimizing transition between floors and can be installed in combination with underfloor heating. The Mouldblock technology makes it not only moisture resistant, but also mould resistant, as it has no paper facing that could sustain mould growth.
The board presents a perfect substitution for plywood or plasterboard, gypsum boards and glass mesh cement boards, as it will not warp or rot when exposed to water. The innovative EZ Grid recessed fastener pattern makes the installation process even easier.
- Highly water and mould resistant,
- Durable, flexible and cost-effective,
- Easy to cut and snap,
- Especially designed for floors and counter tops,
- Includes an innovative Mouldblock technology,
- Includes EZ Grid recessed fastener pattern for easy installation,
- Minimizes the transition between floors,
- High comprehensive and flexural strength,
- Asbestos, gypsum, glass fibre or formaldehyde free.
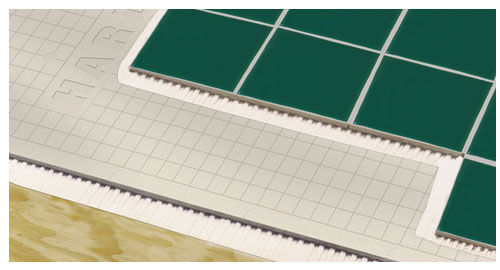
The boards can be easily cut and shaped with carbide tipped scoring knife. A straight edge can be used to score the board, when the board is pulled upwards so it snaps. Once the desired hole size is scored, the weak point within the circle centre should be tapped out with a hammer.
The boards need to be applied onto a clean and flat subfloor, why any damaged, warped or loose parts need to be repaired or replaced. The installation includes a minimum 18mm T&G chipboard or 15mm WBP plywood. In order of preventing cracking of the tiled floor caused by excessive flex, make sure that the floor composition complies with applicable building regulations. The spacing between the joists should not be more than 600mm centres.
The joints can be staggered in a brick or broken bond pattern and should not be aligned with subfloor joints. A 3mm gap between the floor and baths, vanities or wall edges should be properly filled with a high quality sealant. Snap and cut the boards in accordance with the instruction given above. A non-flexible tile adhesive should be added to the subfloor surface using a 6mm notched trowel and the board firmly embedded into the wet adhesive. The boards are fastened with adequate screws or nails, every 200mm, whereas the fixings should be placed 50mm from the corners of the board and 15mm from the edges of the board. A 50mm alkaline resistant Fibatape should be embed across the joints prior to applying the tiles, so it leaves a 150mm wide joint.
When installing the boards onto masonry walls, make sure that the wall surface is dry and clean and the board surface has no settled dust. The back of the board should be covered with high strength cartridge adhesive and pressed firmly onto the wall. The boards are further fastened with stainless steel screws, placed 100mm from the bottom and top edges and 50mm from the right and left ones. Again, a 50mm alkaline resistant Fibatape should be embed across the joints prior to applying the tiles, so it leaves a 150mm wide joint.
- evaluated by the BBA and approved with certificate no. 04/4100;
- in accordance with EN 12467;
- has a class A1 non combustibility rating.