100mm Kingspan Kooltherm K108 Phenolic Cavity Board (pack of 5)
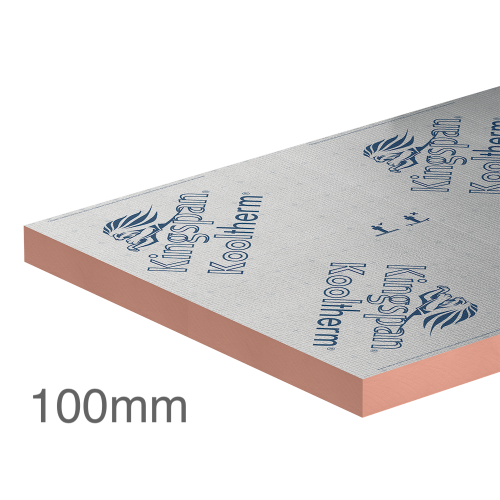
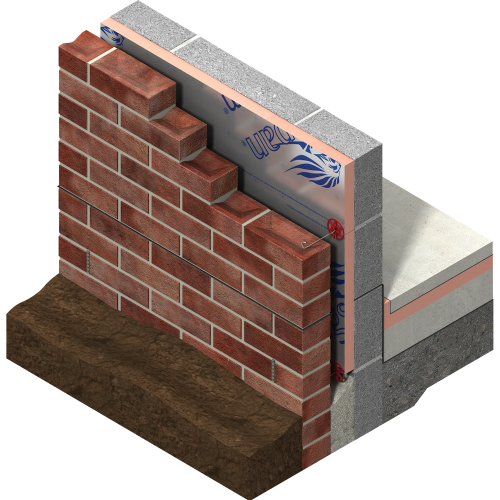
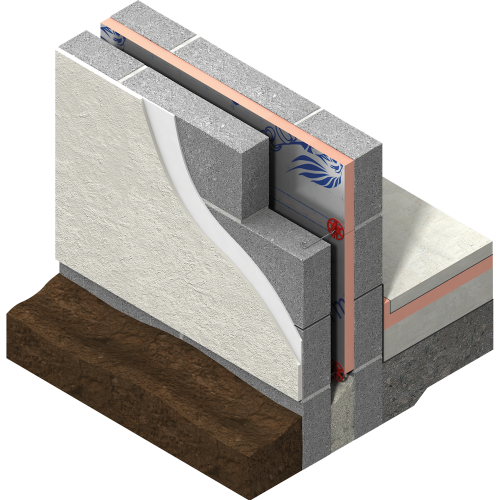



- Product Code: A1-1942
- Delivery Time: 3 - 5 days
- Brand: Kingspan (Tech. support: 01544388601)
- Model and Size: 1200x450mm - 2.70 m2
- Weight: 10.80kg

4.7 out of 5 - Excellent
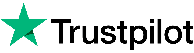

100mm Kingspan Kooltherm K108 Phenolic Cavity Board (pack of 5)
100mm Kingspan Kooltherm K108 Cavity Board features a premium performance rigid thermoset fibre-free phenolic insulation core, which is faced on both sides with a low emissivity composite foil. This product is specifically engineered to minimise thermal bridging and uncontrolled air leakage at junctions in cavity wall constructions. For wall heights of up to 12 metres, a minimum residual cavity width of 25 mm is recommended between the insulation and the outer leaf. For wall heights exceeding 12 metres and up to 25 metres, a minimum residual cavity width of 50 mm is advised. The NHBC accepts a 50 mm residual cavity width for Kingspan Kooltherm K108 Cavity Board across all exposure zones, including areas of very severe exposure to wind-driven rain (exposure zone 4), where the outer leaf consists of fair-faced masonry with tool flush joints.
CHARACTERISTICS
- Rigid thermoset fibre-free phenolic insulation core.
- Faced on both sides with a low emissivity composite foil for enhanced thermal performance.
- Specifically designed to limit thermal bridging in cavity wall constructions.
- Minimises uncontrolled air leakage at junctions.
- Approved for a 50 mm residual cavity width in all exposure zones.
- Suitable for areas of very severe exposure to wind-driven rain (exposure zone 4).
- Designed for use with outer leaves of fair-faced masonry featuring tool flush joints.
- Easy to handle and install.
- Resistant to short term contact with petrol and with most dilute acids, alkalis and mineral oils.
- Resist attack by mould and microbial growth and do not provide any food value to vermin.
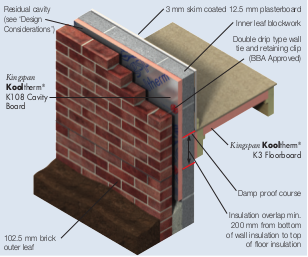
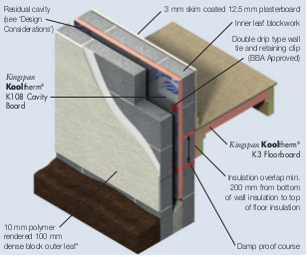
- Kooltherm K108 Cavity Board is typically held in position by wall ties that connect the two skins of masonry.
- Wall ties should include a retaining disc with a thickness of less than 10 mm.
- For a solid concrete ground floor:
- The first row of wall ties is installed in the inner leaf at 600 mm horizontal centres.
- Ties should be a minimum of one course of blockwork below the damp proof course or 150 mm below the top surface of the ground floor perimeter insulation upstand, whichever is lower.
- For a suspended timber floor:
- The first row of wall ties is installed in the inner leaf at 600 mm horizontal centres.
- Ties should be a minimum of 200 mm below the top surface of the ground floor perimeter insulation upstand.
- Continue constructing the inner leaf up to the next wall tie course, typically 450 mm above the first (usually two block courses).
- The next course of wall ties is positioned at the usual 900 mm horizontal centres.
- Install the next course of blockwork to secure the ties.
- The first row of insulation boards should be installed between the two rows of wall ties:
- Ensure each insulation board is retained tight against the inner leaf with lightly butted joints.
- Each board should be secured at a minimum of three points.
- Apply a self-adhesive breathable tape, no less than 100 mm wide, to all horizontal and vertical joints, board edges, and abutting junction interfaces:
- The tape should be applied smoothly and wrinkle-free, extending no less than 50 mm on either side of joints, board edges, and abutting junction interfaces.
- Maintain the seal at protrusion locations, e.g., wall ties.
- Build up the outer leaf to the level of the top of the boards and repeat the process.
- When insulating a gable, continue insulation boards 200 mm beyond the height of the top storey ceiling and install a cavity tray above the insulation.
- After raising each section of the inner leaf, remove excess mortar and clean mortar droppings from exposed edges of the installed insulation boards.
- Use a cavity batten or cavity board to protect board edges and maintain a clear cavity.
- At the end of each day's work or whenever work is interrupted for extended periods, protect board edges and joints from inclement weather.

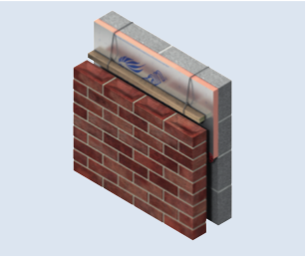
- ISO 9001: 2015 (Quality management systems),
- ISO 14001: 2015 (Environmental management systems),
- ISO 37301: 2021 (Compliance management systems),
- ISO 45001: 2018 (Occupational health and safety management systems)
- ISO 50001: 2018 (Energy management systems).